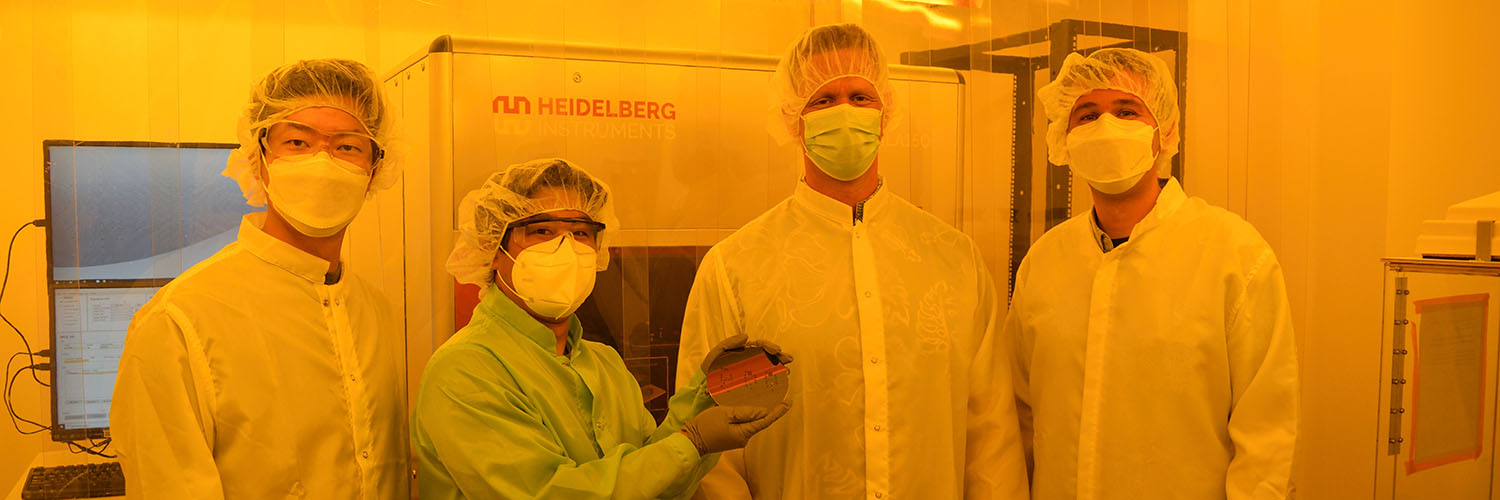
State-of-the-art Microfabrication arrives in Hawai’i
The completed installation of a state-of-the-art tool for advanced manufacturing of small-scale structures inaugurates a new era for the University of Hawaiʻi at Mānoa Clean Room. This new maskless lithography tool, an MLA150 system from Heidelberg Instruments, was delivered and installed at the end of May 2021. This tool uses ultraviolet light to rapidly generate intricate patterns with details smaller than the thickness of a red blood cell (~1 micrometer) across an area the size of a coffee saucer in just a few minutes. This capability allows graduate students, faculty, and other researchers in Hawaiʻi to eliminate days of tedious, expensive work and focus on creation and testing of new research ideas.
“This machine has arrived here as a result of significant efforts by many people across the University. We hope that it will prove to be a cornerstone in the UH clean room for energized research and training activity in microscale and nanoscale science and engineering,” said Joseph Brown, team lead and assistant professor of Mechanical Engineering at UH Mānoa.
This $563k tool was primarily supported by a $466,902 grant from the National Science Foundation (NSF). This funding was raised by a research team from the University of Hawaiʻi at Mānoa College of Engineering, led by Prof. Brown. The UH team also includes mechanical engineering professors Woochul Lee, Sangwoo Shin, and Tyler Ray; and electrical engineering professor Aaron Ohta. The award was part of the highly competitive NSF Major Research Instrumentation program and was one of 155 issued in 2019 totaling $82.66 million.
The arrival of this high-speed, maskless lithography tool is critical for advancing UH Mānoa’s research in engineering, biosciences, and applied physics. Some projects planned by the research team using the new tool include better processes for water purification and medication delivery; microphones narrower than a hair for hearing aids and other applications; tiny pressure, temperature, and humidity sensors for environmental monitoring; improvements to electronics manufacturing; new ways to manage heat and generate electrical power; and wearable flexible electronics for continuous health monitoring.
In addition to significantly expanding research capabilities, this tool provides new research opportunities in microfabrication and nanoengineering to help train the high-tech workforce of the state of Hawaiʻi through hands-on student research projects and enhanced outreach activities. An initial cohort of 15 people including professors, graduate students, and staff, was trained at the startup of the MLA150 machine, Figure 1. The research team is working to establish more robust practices for training and access to the clean room and the lithography tool, and anticipates further outreach activity highlighting this tool in the upcoming academic year.